BioDiesel Production
How Diatomaceous Earth Plays a Critical Role
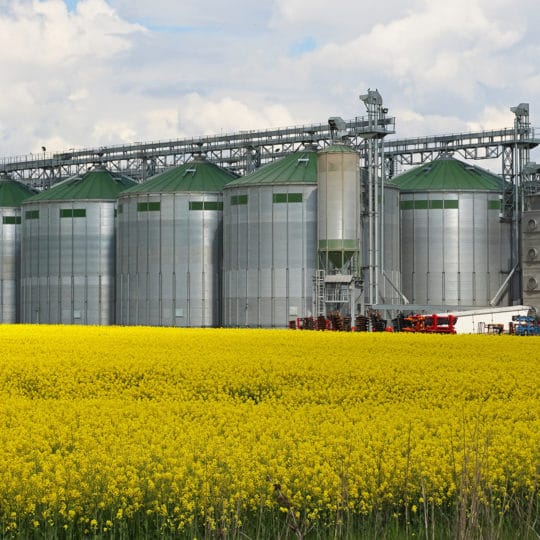
Biodiesel is an alternative fuel source that can be used as a replacement for conventional, fossil diesel. Feedstock choices include pure vegetable oil, animal oil, animal fats, and waste oils. In order to be used as fuel, the oils need to be converted to biodiesel in a process called transesterification. Environmentalists are excited about the possible benefits of this natural fuel option.
One concern about the biodiesel industry is that the fuel offerings are limited to feedstock availability. Promising experiments are underway to maximize the production of natural oils in plants. Scientists at Brookhaven National Laboratory have partnered with schools and identified an enzyme in plants called ACCase that determines the rate of oil production in oilseeds. This enzyme is made of four subunits, and the key to more oil production was found in one of the subunits. When one of the inactive subunits took the place of an active subunit, the cells with combinations of disabled genes didn’t turn off oil production. This new component was named BADC (biotin attachment domain-containing proteins), and it seems to be the key to higher oil production. In-depth studies are being conducted into how this can be applied to crops. Seed companies will soon have the opportunity to test out and study the crops produced with these modified qualities.
Obtaining natural oil is the first hurdle; the second is to produce the biofuel. Today, we’re going to look at an important step in the production: filtration.
The Importance of Biodiesel Filtration
In the mid-2000s, many of the biofuels sold did not meet quality specifications. The Vehicle Technologies Office partnered with the National Biodiesel Board to improve specifications and ways to manage standards. The problem was that solids found in biodiesel oils clogged fuel filters and stopped the flow of fuel to the engine. Now there are standards for filtering these products. Phosphorous and soaps are two main impurities targeted for removal. These impurities are created during the process of neutralizing free fatty acids.
When biodiesel is made, soap is produced as a by-product when free fatty acids in the oils mix with water and catalyst. Generally, the higher the free fatty acid level, the higher the soap content. It is considered a contaminant, and one of the biggest concerns is how to clog fuel filters. It congeals in the filter fibers, reducing throughput, causing clogs, and increasing the time it takes for producing. Plus, when soap burns, it leaves behind an ash residue in your engine.
Phosphorus is another concerning material that needs to be filtered. It can be found in plant oils because of the use of phosphorus-containing fertilizer. Phospholipid compounds can greatly impair the effectiveness of emission control systems. The effects are cumulative, so over time, even trace levels can cause severe damage.
Oil can be filtered in different ways, depending on the clarity you desire for the final product and the ease of use versus productivity you require. Some common methods include settling, bag filters, cartridge filters, leaf and filter presses utilizing diatomaceous earth.
Diatomaceous Earth for BioDiesel Filtration
Diatomaceous earth, also known as diatomite and DE, is the naturally occurring fossilized remains of diatoms—single-celled aquatic algae. Diatomite consists of billions of minute silica frameworks, making it an ideal filter media.
Using a filter media is important because it prevents the cloths used in a filter press from being blinded, which happens when too many particles are collected and oil can no longer pass through. To prepare the filter press for filtering, a mixture of clean oil and diatomaceous earth is pumped quickly into a stack of cloth-covered plates pressed tightly together. This mixture deposits the filter media onto the cloth, creating a buildup of about 1/16″.
- For a 1/16″ buildup on the plates, use 68 grams of diatomaceous earth per square foot of filtering cloth area.
- The quantity of oil to use is determined by the volume of oil held in the press. The press manufacturer often provides specifications for this.
Once the plates are coated with diatomaceous earth, you can start filtering the oil to be cleaned.
- The filter press pump holds constant pressure on the oil/sediment slurry being filtered. Do not let the pressure of the filter press drop to zero when switching from one source to another because it is possible for the filtering media to slough off and drop to the bottom of the filter press cavity.
Filter media can also be added to the bulk of the oil being processed before it passes through the filter press. This increases the time it takes for the liquid to be filtered.
Choose Dicalite for Your BioDiesel Filtration Needs.
The mineral experts at Dicalite Management Group know the ins and outs of using diatomaceous earth for filtration. We know you’ll love it too, so we’d like to send you a free sample. Our customer service representatives located at our plants are standing by, and our technical experts are anticipating your call. Call us today at 866-728-3303 for your free sample and to see for yourself what makes Dicalite Management Group a customer-first industrial minerals company.
If you’d like to learn more about using minerals for filtration, download our free e-book A World of Filtration Experience today.
Join Our Mailing List
Our blog offers insight and information about new and exciting uses for perlite, diatomaceous earth, and vermiculite deriving from years of research and application. From passive fire resistance to mineral depth filtration, by subscribing to our mailing list, you will receive the latest information surrounding the Dicalite, Dicaperl, and Specialty Vermiculite brands and products.